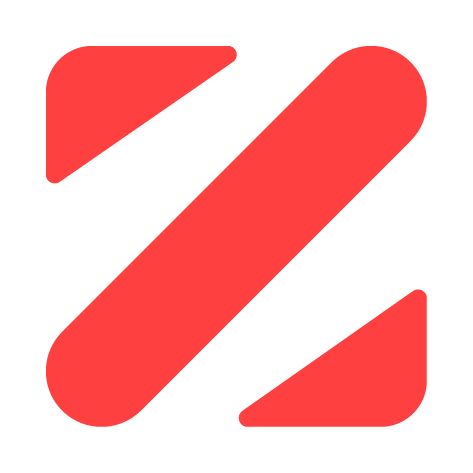
Continuous Caster
The Continuous Caster represents a key element in many steel plants. It has a direct impact on the productivity of the plant, but also on the product quality. As it still involves operations with hot, liquid steel, the integrity of the continuous caster also can have a significant impact on the safety of the workers on-site.
In reality the continuous casting installation consists of multiple sections. On the one hand there's the caster ladle turret, relying on its bearing to rotate the ladles around. Next to that there's the tundish and mold combination where the liquid steel gets shaped and last in line is the continuous casting line, a set of rolls where the material is cooled unti it is sufficiently solid to engage in subsequent process steps.
How is the integrity of the caster managed today? Most often based on technical data sheets coupled with the knowledge of a number of unique experienced individuals in the plant and the maintenance plan provided by the supplier. Interventions are done on regular intervals, or when something happened. All of this puts tremendous strain on the people responsible for keeping the installation running, while it can be avoided, quite easily. Also, in rare cases, more far-reaching events occur. Some more regularly, such as a breakout, and others less frequently, but very dramatic, such as a failing foundation or swivel bearing. A resulting spill of liquid metal can have lethal consequences and is of course to be avoided.
The only way to validate the actual health of such an installation is by having a continuous look at a broad data set and adding a specific multi-aspect monitoring setup consisting of different sensor types that follow the behaviour of the general state-of-health of the different parts in the Continuous Caster installation.
We understand the problems you face
Identify problems before they cause greater damage, improve your process!
Slewing or Swivel bearing health
Every time the ladle has been emptied, the tower is continuously, but slowly, rotated 180° around its central axis. The structure, and more specifically the swivel or slewing bearing, can suffer from extensive degradation, locally, or over a more extended section. A dedicated monitoring, coupling process information such as weight of the charge and rotational angle with data generated through high- frequency, high-sensitivity 3D accelerometers, current coils, inclinometers and temperature probes in a smart way provides a way of continuously, tracking bearing health.
Foundation health
in a number of cases the tower is attached to a concrete foundation massive using so-called anchor bolts. These take up all the loads taken up by the tower. When they fail, the tower may collapse. Monitoring bolt tension and or local displacement with an adequate system can serve as an adequate early warning system to detect potential structural integrity issues well ahead of time.
Segment alignment
A continuous casting line usually consists of multiple segments in series. This allows for flexibility during operations, but the alignment between segments and their internal geometry (rolls and bearings) can give rise to premature damage or process distortions. By continuously monitoring accelerations, motor currents, positions and/or mounting forces (bolt tension) at high frequency, non-idealities can be identified and localized in an early stage. Roller or bearing (house) damage can be identified in an early stage. As such significant damage can be avoided and availability can be tuned to a maximum.
Line motor health
Motors are essential for moving the cast through the segments. Although some redundancy is often available, failure or malfunctioning is best predicted well in advance. Also the way the cast moves through the line can influence the health of the motor, by for example inducing additional friction or shocks due to a distorted operation. Combining a follow-up based on vibrations in multiple axes, temperatures and electrical currents the state-of-health of the motors can be tracked continuously, deviations detected in an early stage and unwanted standstills prevented.
Process deviations
When in operation, the casting process is ideally as smooth and continuous as possible. Each deviation might result in product quality issues or sub-optimal production speed. Combining process parameters, material properties and cooling system, a smart algorithm allows to continuously track the casting process. In case of deviations in the process, the operator is warned and can take preventive measures to avoid a noticeable impact on production.
Oscillator health
The oscillator is essential in the process, as it avoids that the cast gets stuck during the initial phase of the operation. Continuously tracking the vibrations in 3 axes allows detecting deviations in an early stage: blockages, issues with mounting, shifts in mass balance...
BEARING HEALTH | COUPLING HEALTH | COOLING PROCESS STABILITY
Compatible with:
Our monitoring products are compatible with installations of the following suppliers:
- Primetals
- SMS
- Sarralle
- Sama
- ...
Software integrations:
All of Zensor's products are compatible with standard CMMS or EAM software. Connections can be set up to source the most recent interventions and changes on the asset, or to create a ticket when an intervention is required on a section of the rolling line. Compatible with:
- IBM Maximo
- IFS Ultimo
- eMaint CMMS
- Aveva
- SAP
- iba
- ...
Solutions
Learn more about our approach
Performance
Based on the data collected and machine-learning based methods for determining the operational condition the performance is calculated.Quality
Coupling to existing databases or using human input fields the product quality is linked to operational process parameters.Warnings
Whenever values start to deviate, or data streams stop, warnings are sent. This avoids 'black holes' in the insights of the production line or assets.Increase availability
Have a continuous idea of availability, automatically as the platform combines different input streams and contextual information.Our Experiences
Conferences:
EEC 2024
Essen, Germany
Zensor presented some of its findings in EAF monitoring during the EEC conference.
Projects we work on:Saarstahl
Neunkirchen, Germany
Zensor works with Saarstahl to optimise their wire rolling mill by understanding the damaging conditions affecting their components.
Projects we're working on:Aurubis
Olen, Belgium
Zensor are proud to be working with Aurubis to help optimise their cooper wire rolling mill. Results to share soon...
Blog post:Experience at Hüttentag
Last week Zensor attended the Hüttentag in Essen. During this annual event the entire German steel industry meets up to discuss the state of affairs and exchange ideas about upcoming developments and changes.
Looking for another asset?
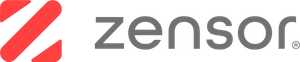
Zensor NV
BE0537837878
© 2025