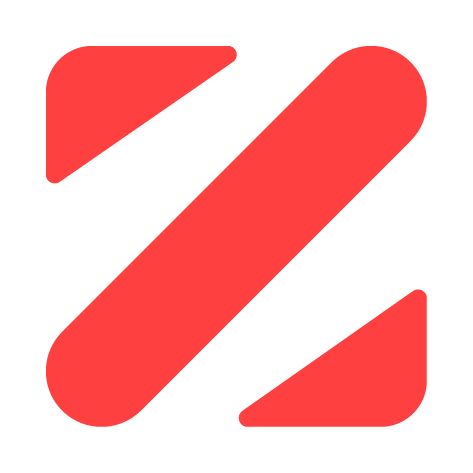
EAF (Electric Arc Furnace)
Unexpected shutdowns are costly and very demanding for the workforce involved. Make your EAF smart in order to increase the availability and quality output.
Today most often technical data sheets coupled with the knowledge of a number of unique experienced individuals are used to determine when maintenance is required for the EAF. Interventions are done on regular intervals, or when something happened. All of this puts tremendous strain on the people responsible for keeping the installation running, while it can be avoided, quite easily.
The only way to validate the actual health is by having a continuous look at a broad data set and adding a specific multi-aspect monitoring setup consisting of different sensor types that follow the behaviour of the general state-of-health of the EAF and its components.
We offer modular monitoring solutions for specific aspects that can affect availability and integrity of Electric Arc Furnaces. The different aspects are highlighted in the section below. Our monitoring solutions are end-to-end, which means they cover the entire scope: from sensors and acquisition hardware up to data management, continuous analysis and reporting. Warnings are sent when things threaten to go wrong.
We understand the problems you face
Identify problems before they cause greater damage, improve your process!
Slewing or Swivel bearing health
A gantry is used for moving the electrodes in and out the bath and/or for operating the lid of the reactor. The structure, and more specifically the swivel bearings also can suffer from extensive degradation. A dedicated monitoring coupling information about high-sensitivity acceleration data, electrical currents, inclination and/or temperatures in a smart way provides a way of continuous tracking gantry (bearing) health
Electrode health
The electrodes are used to transfer the electrical energy into the furnace and start melting the metal. During this process, the electrodes undergo a lot of force. Based on the properties of the primary materials and the process parameters, the integrity of the electrodes or their support structure can be affected. Coupling information about vibrations, currents, inclination and/or temperatures in a smart way provides a way of continuously tracking electrode health.
Busbar health
Busbars are used to transfer electrical energy to theelectrodes. Due to the high currents involved this
results in high vibrations and inductive coupling to
other components. Monitoring of vibration levels and
temperatures allows to reduce the chance for
resulting mechanical or thermal damage.
Structural dynamics vs. Process parameters
The melting process is a function of various operational parameters: electrical currents, composition and mechanical properties of primary materials, gas flow, vibrations, temperatures... Tracking all relevant parameters allows building up models separating 'normal' from 'abnormal' behaviour. Prolonged follow-up in turn allows identifying and quantifying changes in dynamic behaviour for similar process conditions, leading to early detection of damage development or process issues.
Process deviations
Using the data available in the Historian or SCADA system the operation of the EAF is continuously parametrised. Of interest are for example water flows, temperatures, electrical currents... The different stages of the process are automatically identified and when properties start deviating or unexpected values are detected, a warning is sent. The follow-up is based on process knowledge as well as models trained on the behaviour of the specific asset followed.
Hot Heel / Liquid Heel
The goal of an advanced monitoring solution is not only to predict failures and detect degradation in an early stage. When done in a smart way, also the process can be optimized. Depending on the strategy of operating the EAF, it can be important to know if yes or no a liquid heel is present in the vessel after tapping and the amount of material it represents. Using the appropriate data treatment the amount of material can be derived from the dynamics of the system.
COOLING SYSTEM HEALTH | POURING PROCESS DEVIATIONS
Compatible with:
Our monitoring products are compatible with installations of the following suppliers:
- Primetals
- SMS
- Danieli
- Tenova
- Sama
- ...
Software integrations:
All of Zensor's products are compatible with standard CMMS or EAM software. Connections can be set up to source the most recent interventions and changes on the asset, or to create a ticket when an intervention is required on a section of the rolling line. Compatible with:
- IBM Maximo
- IFS Ultimo
- eMaint CMMS
- Aveva
- SAP
- iba
- ...
Solutions
Learn more about our approach
Performance
Based on the data collected and machine-learning based methods for determining the operational condition the performance is calculated.Quality
Coupling to existing databases or using human input fields the product quality is linked to operational process parameters.Warnings
Whenever values start to deviate, or data streams stop, warnings are sent. This avoids 'black holes' in the insights of the production line or assets.Increase availability
Have a continuous idea of availability, automatically as the platform combines different input streams and contextual information.Our Experiences
Conferences:
EEC 2024
Essen, Germany
Zensor presented some of its findings in EAF monitoring during the EEC conference.
Projects we work on:Saarstahl
Neunkirchen, Germany
Zensor works with Saarstahl to optimise their wire rolling mill by understanding the damaging conditions affecting their components.
Projects we're working on:Aurubis
Olen, Belgium
Zensor are proud to be working with Aurubis to help optimise their cooper wire rolling mill. Results to share soon...
Blog post:Experience at Hüttentag
Last week Zensor attended the Hüttentag in Essen. During this annual event the entire German steel industry meets up to discuss the state of affairs and exchange ideas about upcoming developments and changes.
Looking for another asset?
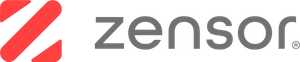
Zensor NV
BE0537837878
© 2025