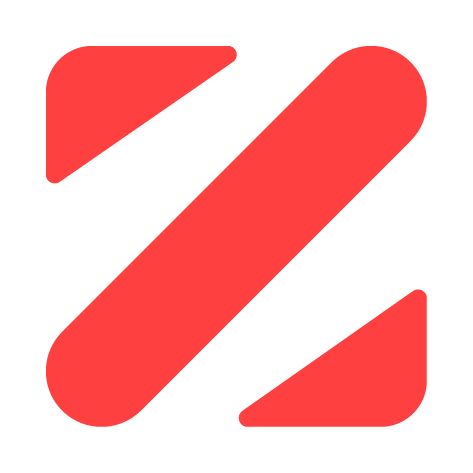
Energy
A site is running optimally when it can produce the maximum amount of goods in the most sustainable way: with a minimal energy consumption. All too often however processes run in an inefficient way or losses aren't detected. This relates to electricity consumption, but is valid as well for compressed air, cooling as well as heating systems. Through the same platform leaking valves and inefficient process steps can be detected and identified.
Combining the follow-up of the installations and processes together with their energy consumption represents a great tool to achieve a sustainable and cost-efficient production.
All data is gathered in a single location and translated into insights:
- Detecting losses and trends
- Detecting inconsistencies and deviations
- Daily, weekly, monthly reporting
- Closely watching overall consumption
- Identifying highest consumers
- Generating real smart insights, not just consumption graphs
- Tracking how operations and/or assets are linked
All using data from existing sensors and databases, and adding extra sensors and readout units when required: minimal upfront investment
Combining all relevant utilities: gas, electricity, fuel, water, compressed air, heat...
We understand the problems you face
Catch them before they cause greater damage!
High energy costs
Production requires energy, energy is not available for free. Minimizing the energy losses and overall consumption leads to a more profitable operation.Unknown losses
It is often known that 'energy is an important cost', but seldom one has identified where the exact sources of this cost lie and where the best opportunities for improvement are found.Sustainability it an issue
High energy consumption means a high energy need per unit (of mass) produced. When this number can be reduced, your production (and product) becomes more sustainable.Not an isolated story
Monitoring and tracking energy consumption in a production site results in much more than mere energy bill reductions. It also allows identifying inefficiencies in the production process and forms a tool to identify deviations in an early stage: more savings ahead.Solutions
Learn more about our approach
Performance
Based on the data collected and machine-learning based methods for determining the operational condition the performance is calculated.
Quality
Coupling to existing databases or using human input fields the product quality is linked to operational process parameters.
Warnings
Whenever values start to deviate, or data streams stop, warnings are sent. This avoids 'black holes' in the insights of the production line or assets.
Increase availability
Have a continuous idea of availability, automatically as the platform combines different input streams and contextual information.
Our Experiences
Projects we're working on:VUB Jette Campus
Belgium
Zensor is proud to be working with the VUB and Mobi Team to monitor the energy consumption of a student dorm at the Jette Campus in Belgium.
Projects we're working on:EMAX
The Netherlands
Zensor is helping EMAX meet stringent energy consumption targets by monitoring the total consumption over their entire site
Blog post:Energy Crisis: alternative ways to solve present-day problems?
The energy crisis is hitting the European manufacturing industry. Hard. Till a few months ago, labor cost was the largest price driver for base materials and semi products on the Old Continent. Since a few months however the balance has shifted: energy costs represent...
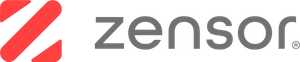
Zensor NV
BE0537837878
© 2025