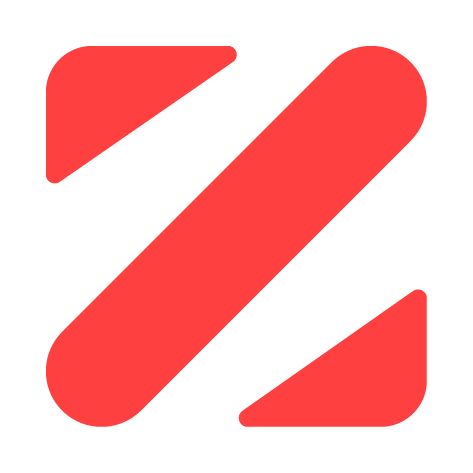
Plate Leveler
Unexpected shutdowns are costly and very demanding for the workforce involved. Make your plate leveler smart in order to increase the availability and quality output.
Today most often technical data sheets coupled with the knowledge of a number of unique experienced individuals are used to determine when maintenance is required the plate leveler. Product quality only becomes an issue when customers start complaining. Repairs are done when it's already far too late. All of this puts tremendous strain on the people responsible for the plate leveler, while it can be avoided, quite easily.
The only way to validate the actual health is by having a continuous look at a broad data set and adding a specific multi-aspect monitoring setup consisting of different sensor types that follow the behaviour of the plate levelers general state-of-health.
We understand the problems you face
Catch them before they cause greater damage!
Roll damage
A damaged roll means your entire production comes to a halt. Continuous monitoring of internal pressures allows preventing excessive local forces, thus roll damage.Product quality
The more perfect the material, the higher its value.A perfect control of the stress distribution within the plate can be reached through permanent monitoring. The associated feedback loop allows generating a maximum amount of top-notch material, coil after coil.Bearing degradation
A huge amount of axes means an equivalently high amount of bearings. When monitoring continuously those conditions that induce excessive damage can be detected and subsequently avoided to maximise bearing life.Motor health
Uneven loading and intermittent operations put serious strain on a motor. Sensor data linked to specific operating conditions allows detecting developing problems in an early stage.Gearbox health overview
A very complex gearbox means complex problems. A permanent follow-up will help detecting misalignments or looseness in a nearly stage and will help preventing major problems as much as possibleYield optimisation
The faster perfectly flat plates can be produced after starting a new coil, the less material has to be thrown away. A smart sensor set helps insetting the optimal set point to begin with and to rapidly reach the perfect conditions for each run.SET POINTS | STRESS DISTRIBUTION | AVAILABILITY STATISTIC
Solutions
Learn more about our approach
Performance
Based on the data collected and machine-learning based methods for determining the operational condition the performance is calculated.Quality
Coupling to existing databases or using human input fields the product quality is linked to operational process parameters.Warnings
Whenever values start to deviate, or data streams stop, warnings are sent. This avoids 'black holes' in the insights of the production line or assets.Increase availability
Have a continuous idea of availability, automatically as the platform combines different input streams and contextual information.Our Experiences
One-pager:Plate leveler
We know your greatest issues and we know how to solve them - check it out.
Blog post:Experience at Hüttentag
Last week Zensor attended the Hüttentag in Essen. During this annual event the entire German steel industry meets up to discuss the state of affairs and exchange ideas about upcoming developments and changes...
Looking for another asset?
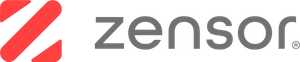
Zensor NV
BE0537837878
© 2025