·
As the post-covid-19 world is finally looming in some European countries, both individuals and organizations alike wonder what is to be learned from this unusual situation. One pivotal point which captured the business’ press attention is the drastic change of working conditions tied to the central role of manufactures and industries in the economy.
The new wave of telecommuting in the EU since March pushed a lot of employees in the manufacturing sector to adapt to a rapidly changing working environment, be it the white or blue-collar workforce. Among other consequences, the lockdown induced by the pandemic minimized the amount of people that could attend the production site to check the situation for sanitary purposes.
In the past months, we changed the way we see distance, the burden of commuting and the benefits of the internet. Working from home has become the new norm and for some people this situation revealed a new array of possibilities in their day-to-day working habits.
Naturally, working from home also comes with drawbacks like a weaker social bond with colleagues and a loss of productivity in the factory but all this can be balanced out easily with the right tools at hand. Just like telecommunication platforms balanced out the loss of social bonds induced by the pandemic;
Lockdown softening phase
Digital tools and the reliance on cloud have a great potential to ensure business continuity during the lockdown softening phase. As most manufacturing businesses are still reluctant to embark on non-core projects, new tools based on the IoT and predictive analytics have a great role to play to support core internal business processes in the factory of companies.
Smart remote site monitoring tools do exactly that. If used properly, they can overcome the burden of social distancing measures while increasing transparency to the relevant decision-makers.
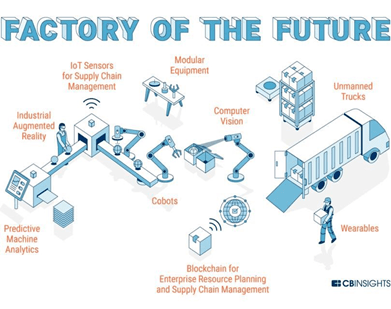
Zensor envisions a smart and sustainable future through predictive machine analysis and IoT sensors
Today and in the upcoming months, strict sanitary conditions are standardized for the common good. The white-collar workforce who is crucial to the proper functioning of the production line (e.g. plant managers, maintenance managers and production line managers) could hardly work on site the same way they did before. Throughout the lockdown softening phase, this still holds true to a certain extent and it should not be an issue!
With the help of cloud servers and smart equipment on the production line, relevant managers can access a series of easy-to-navigate pre-configured dashboards from home. They are not only useful for the management of the production line but also for the monitoring of long-lasting infrastructures. In any case, we provide recommendations on what to monitor and it tells you everything you need to know in real time. Not only do you have access to what is happening on site without the need to move physically, but remote monitoring also avoids the inconvenient intervention of technicians to report on the status of the production line on a regular basis.
These two benefits hold even more true for businesses operating in globally distributed value chains as managers and employees cannot not be physically present to monitor quality and performance metrics in several factory lines simultaneously. Instead of seeing the current situation as a burden to overcome, one should see it as an
eye-opening situation on the opportunities that the IoT and Industry 4.0 are offering to the production industry.
Beyond the pandemic, the role of green IT
The road forward in the post-covid-19 world and the ‘new normal’ will also come with a lot of uncertainties for the manufacturing and production industries, albeit of different nature. The effects of climate change will gradually force companies to become both more resilient and transparent on their activities. Some industries will need to report on their carbon emissions and their intention to reduce them while keeping their golden rule of reducing operation costs.
The digitization in the factory has all the tools at hand to perfect business metrics, foster end-to-end visibility and ease the process of decision-making while reducing negative environmental impacts. Two examples of solutions that help companies achieve this aim are cloud platforms and remote site monitoring.
First, the gathering and processing of data of the production line on cloud platforms is a much more energy efficient solution than using on-premise servers. According to the 2012
report from the NGO Natural Resource Defense Council and the consultancy WSP Environment & Energy, when a company decides to move its servers from on-premise to a private cloud server it reduces the carbon emissions per GB of data stored by 36.7% on average.
Second, remote site monitoring allows the white-collar workforce to complete a large portion of their activities from home. With the complete setup of sensors on site, they would only have to come to the factory when their presence is needed and not on a regular basis (see left side of figure below). With the help of dashboards and alarms, the travels on site are fact-based and in due course which avoids useless travels and saves emissions.
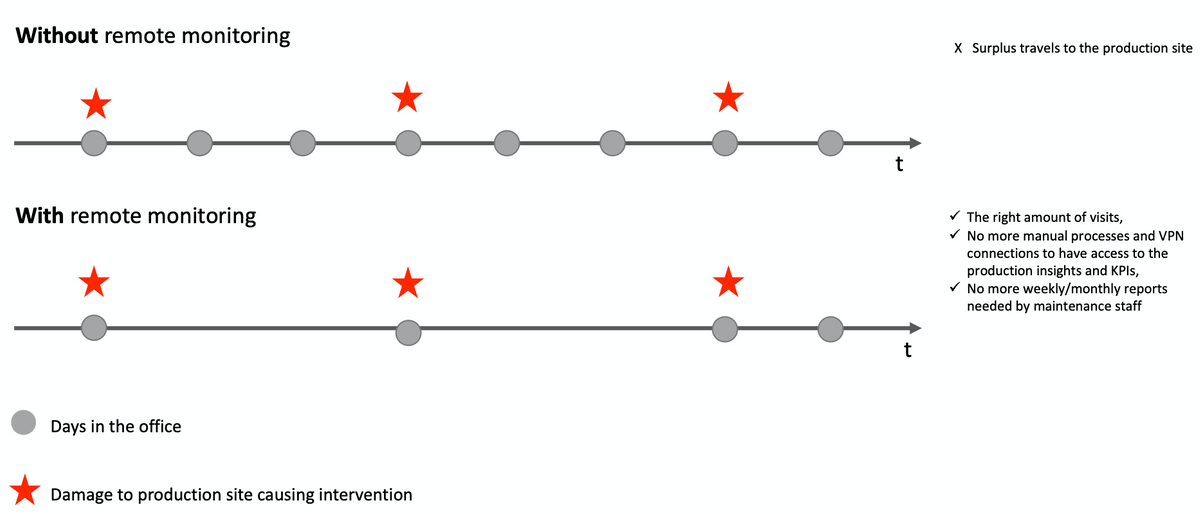
Here’s a little example to illustrate the idea. Let’s assume that 44 people are using Zensor’s remote site monitoring tools today. Let’s further assume that before engaging in a strong partnership with us, these people were going on site to check the situation with technicians once every week. By using the average amount of carbon emissions produced by car (0.2 kWh/km) and the average distance of the round trip to go from home to work for the Belgian population (20.5 km), we have an average amount of energy of 36 kWh needed every day for the regular check-ins. Put another way, using the European average of carbon intensity, Zensor’s remote monitoring solutions would save on average around 9kg of CO2 per day. And keep in mind that this doesn’t even consider the benefits of cloud servers over on-premise servers.
To sum up, remote site monitoring has great potential to overcome the challenges not only of the lockdown softening phase but also by looking at what will happen beyond the current situation. By relying on cloud platforms and the IoT, the tools we offer are useful for both the white and the blue-collar workforce on critical production assets. Remote site monitoring also asserts itself as a useful tool to consider sustainability and cleaner production lines: not only do cloud platforms consume less energy per amount of data stored, but they also allow for less travels on site.
Image Head: Tomasz Frankowski @unsplash.com