Conveyors form a cornerstone of many production plants and processes. The first conveyors have appeared near the end of the 18th century and since then their usage has only increased. Their usage can be found in roughly 2 kinds of operations. In the first they are conveying goods or materials between 2 locations or process steps, such as the conveyor belt transporting the iron ore into the blast furnace in the steel plant, or the chain conveyor moving the malt from the germination chamber to the drying kiln. In the other cases they represent an intrinsic part of the process, for example the belt used for transporting waffles at the right speed through a tunnel oven for baking them till nicely brown and crisp.
Conveyors (excluding screw conveyors) work around a similar principle, a chain or belt (a rubber with embedded fibers or steel wires, or a mesh of plastic or metallic shackles) is moved around 2 extremities: rotation points, drums, pulleys or sprockets. At at least 1 side the motion is introduced: there the pulley, sprocket is connected to a motor or motor-gearbox combination. In some cases the belt is supported by a set of rolls (idlers), in yet others the chain is moving freely (scraping) over a surface. The tension on the belt or chain of the conveyor is often controlled. In that case a tensioning device is used, sometimes based on a screw principle, in other cases by tensioner rolls using gravity. Sometimes also a cleaner or scraper is used if the material moved could stick to the belt. To conclude one will find a set of bearings in almost every conveyor, ensuring that all rotating parts can run smoothly.
Why would you want to monitor a conveyor? A first selection criterion is based on the criticality of the conveyor. If the conveyor is not critical for the process, can be easily replaced, or if all spare parts are abundantly available, the business case for monitoring is not that strong. If however the conveyor is critical for production (like in those that form an intrinsic part of the installation or production line), when spare parts are too expensive to keep in stock, or when a component replacement requires a long and expensive preparation, a solid monitoring often is a good idea.
When asking what to monitor, one would often bring up classical component monitoring, such as motors, bearings or gearboxes, using high frequency accelerometers. This can be done through regular checks (manual measurements) and spectral analysis, or even by a continuous, automated follow-up. There’s however much more relevant stuff to be done. When tracking an individual component this way, one will detect damage in an early stage, but won’t be able to prevent this damage (= detect phenomena that lead to damage, before actual damage happens). Also it is very hard, to impossible, to automatically determine the mechanism at play in such case.
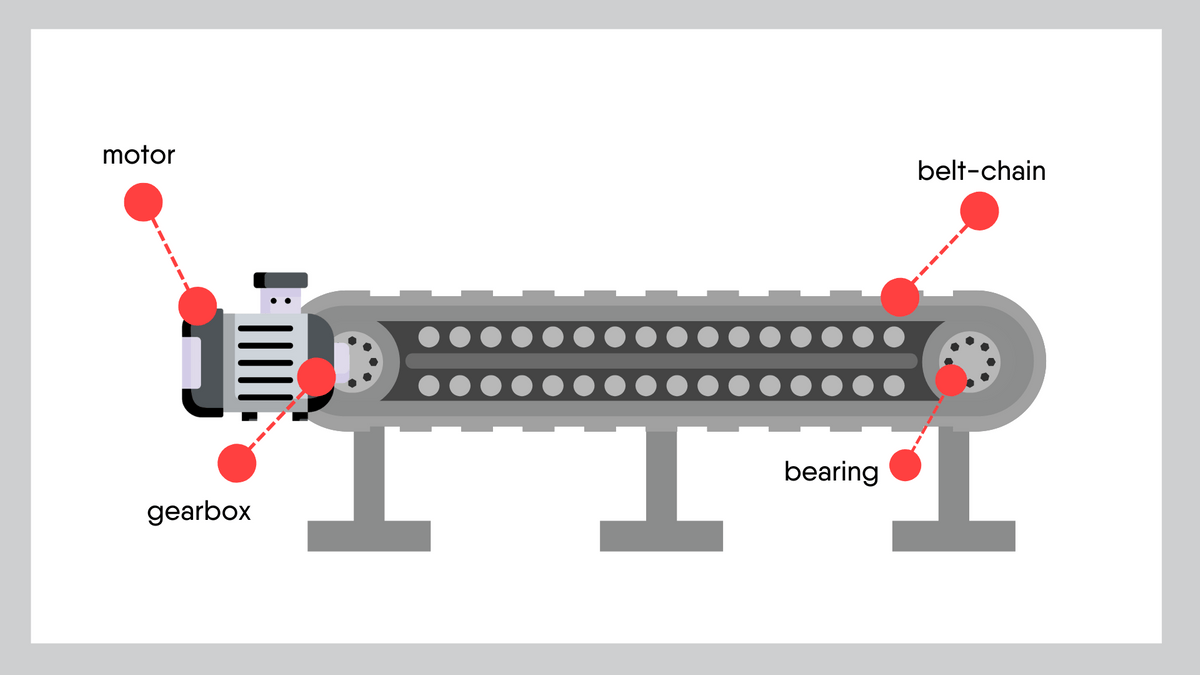
Alternatively one can choose to look at the conveyor as a system, and design & implement the monitoring solution with this in mind. To use the full potential of such kind of monitoring, it should also be automatic and continuous. In that case one would also include monitoring of the belt or chain tension (e.g. by load cells on tensioners) together with electrical current and potential of the motor. The monitoring system for example knows the rotation speed of the conveyor. If irregularities are noticed in the belt tension that occur at the same frequency as a full rotation of the belt, this probably indicates a deformation or other damage to the belt, or accumulated material. When comparing the spectral content of the tension levels at both sides of the belt, one can even detect issues with the straightness of the belt or chain. Detecting and acting on these issues in an early stage is an illustration of what ‘predictive’ maintenance should really be. In many cases this term is used to indicate approaches that are able to detect or identify damage in an early stage. When one can detect operational deviations early on, it is however possible to prevent operational conditions that lead to that initial damage. A much more efficient way of reducing maintenance costs.
Following the same approach on will also be able to detect gradual tension loss in an early stage. This is very valuable as well, as correcting this will ensure a longer life for the belt or chain, but also is beneficial for energy consumption. An other phenomenon seen sometimes is related to the motor current going up on irregular moments in time. This is often indicative for material blockages or other friction in the conveyor. When tension fluctuations occur at the same frequency of a drum or idler roll, this is indicative for upcoming damage in one of these components: this is an example where an indirect measurement combined with smart data analysis can tell something about a remote component.
In applications where there’s a danger for explosion, for example in high-dust locations, bearings are often instrumented with temperature sensors of the PTC type: if the temperature exceeds a certain threshold, the line is stopped. This is of course great for safety, as a potential disaster can be avoided, but an unforeseen and sudden stop is much to be avoided when looking at the operations from the point of continuous and cost-efficient production. Also this can be done much better when applying smart and continuous monitoring. Equipping the required bearings and components with Pt100 or other classical temperature sensors and ensuring a continuous data acquisition and analysis allows one to harvest much more insights from the same system. At first one can see, through trend detection, when temperatures at an individual bearing are increasing. This will trigger an alert and a technician can be sent over to evaluate the situation hours before the threshold would be reached. The minimal gain is that during that inspection for example some material accumulation is seen that can be easily remediated. At this point an unforeseen stop was avoided, so also the associated production loss or delays in (un)loading, as well as all the stress associated with looking for the cause or origin of the stop, not seldomly happening in the middle of the night, or in the weekend.
As this follow-up is continuous and takes place on all relevant bearings in parallel, a lot more can be done. In some cases, as a result of maintenance or after an intervention, the temperature sensors get and remain removed from the bearing after a re-start. In the classical situation this would go unnoticed almost all of the time, creating a point of risk, as one bearing is in practice un-monitored. The smart monitoring would detect these cases immediately, as the temperatures measured on the associated after the restart would be lower than those that the model expects. The third use of this same data is purely maintenance-based. The model trained to track the different temperatures will also detect limited temperature increases on individual bearings. These are often indicative for interior damage development. Although the damage is in htat case often already in an advanced phase, we’re most of the time well ahead of failure. As such a short repair can be planned in, replacing the degrading bearing, and the conveyor can continue working in optimal conditions.
In conclusion we can say that various types of conveyors are encountered in multiple production and manufacturing sites. Some are less critical, and can be taken care of in a classical way. When the conveyor belt, reddler or elevator is however critical in the process or is hard to intervene on, a smart monitoring based on smart data analysis can bring a lot of added value. by combining data coming from multiple sensor types, from different locations and in a continuous stream, multiple phenomena and problems can be predicted or detected. This will result in lower stress for the maintenance team, less interruptions in production, cost savings and even a lower energy bill.